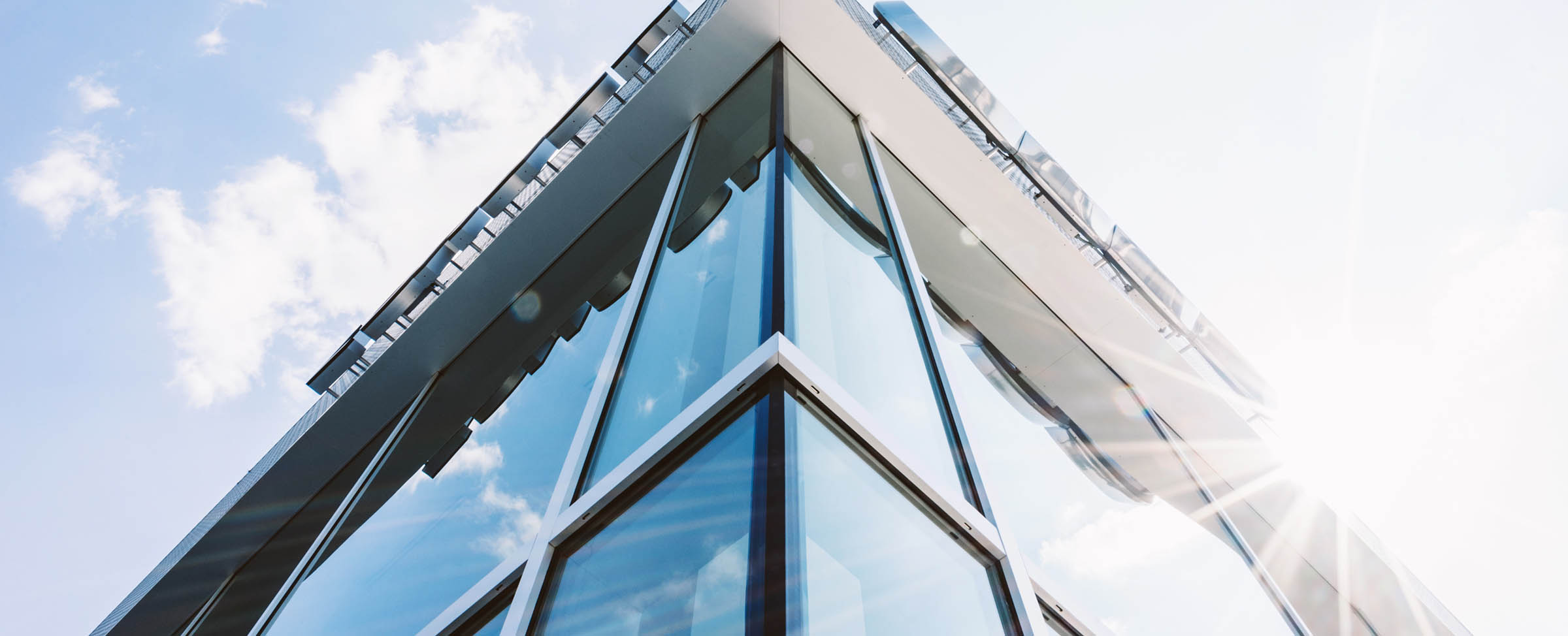
The demand for light and ultra-strong means of suspension is constantly increasing. In many maritime applications, ropes made of HM-HT fibres (high modulus-high tenacity) have already become state of the art. The tensile strength values of these ropes clearly exceed those of conventional steel ropes. We have also successfully achieved tensile tenacity at the level of that found in steel ropes thanks to the so-called thermofixing procedure.
Effects achieved from thermofixing textile means of suspension:
- approx. 30 % higher tensile strength
- approx. 35 % higher Young’s modulus and
- approx. 85 % less structural elongation
The thermofixing process is only economically feasible up to a maximal rope diameter of 20 mm. For a 10 mm diameter rope, thermofixing takes approximately 18 minutes. It takes 30 to 50 minutes for a 20 mm rope. When the rope is heated, a temperature gradient appears from outside to inside, and, as a result, the rope is fixed heterogeneously. The outer regions reach the fixing temperature and are fixed very quickly, whereas the inner regions are fixed much later or remain unfixed due to the poor thermal conduction in the fibre materials. When thermofixing by means of a forced-air oven, a heterogeneous strength curve arises.
Using the TEXELMA technology, ropes can be fixed through the whole cross section – independently of the rope diameter – in less than 2 minutes. This procedure contributes to higher product quality, since the fibres at the rope surface are fixed at the same time and temperature as inside the means of suspension. Second, production time is greatly reduced, and, as a result, production costs drop significantly. Moreover, ropes of more than 20 mm diameter can now also be easily and quickly thermofixed.
Objective conflicts
- Without TEXELMA, at present, it is impossible to finish a textile-based fibre rope with a lubricant percentage higher 5 % with a thin-walled monolithic extrusion casing. This is due to the fact that the coating components become gaseous due to the high temperatures of the polymer melt and cause gas bubbles to form in the casing. The lubricant deposited on the rope surface also works against a reliable, slippage-free core-casing-bond. As a result, the service life in comparison with a lubricated rope is multiply reduced.
- Braided traction media are characterized by great initial elongation induced by conventionally applied extrusion casings (retracting spring). TEXELMA solves this problem by using a multi-step stretching process.
- Because of material-specific properties (low transverse strength, low UV-resistance), only ropes whose core is covered by a casing are technically feasible. The casing protects the traction rope against external influences and is the interface between the driving disk and the rope in the case of traction applications. However, it is more difficult to heat through these core-casing designs, and, as a result, a downstream thermofixing process (reducing initial and working elongation) is only possible under certain conditions. TEXELMA has solved this problem, too: the inner and outer rope regions are heated simultaneously.
- Thermofixing the core rope before the casing extrusion causes the lubricant to be emitted from the rope cross section (dry running) and simultaneously to be built up on the core rope surface (reduced bonding of the casing). Thanks to TEXELMA, thermofixing is performed only after applying an extruded casing.